Success Stories
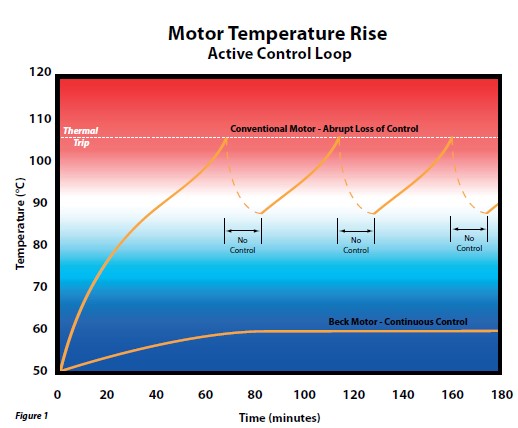
ACTUATOR PERFORMANCE SIGNIFICANTLY IMPACTS BOILER CONTROL & PLANT PERFORMANCE
Harold Beck and Sons, Incorporated has been manufacturing electric actuators since 1936. !e unique design of Beck actuators has made them a standard for modulating damper and valve applications in the North American power industry. This design is specially suited for precision modulation and control without duty-cycle limitations or high maintenance requirements.
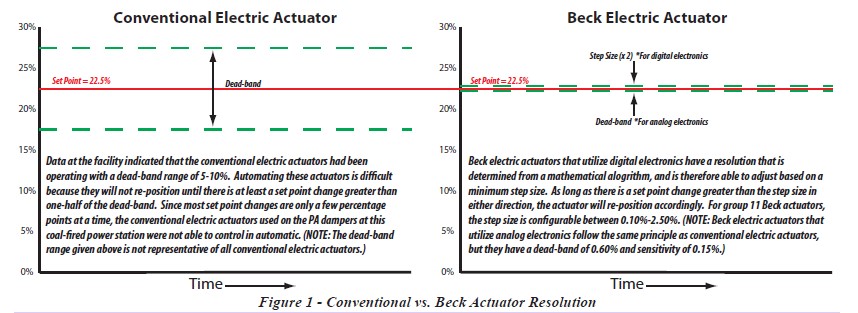
Precise and Reliable PA Damper Actuators have been Improving Automatic Load Dispatch Response at a JEA Generating Station for Over 10 Years
Electric utilities must regulate power production in response to changing demand. The ability to do this rapidly and efficiently is a valuable asset that requires precise, efficient boiler combustion control; however, obtaining the requisite control can be a challenge, even at steady state. Fuel and combustion air flow are controlled by modulating a variety of fans and dampers, and without actuators capable of positioning the dampers precisely, it is impossible to achieve the precise combustion control required for automatic load dispatch.
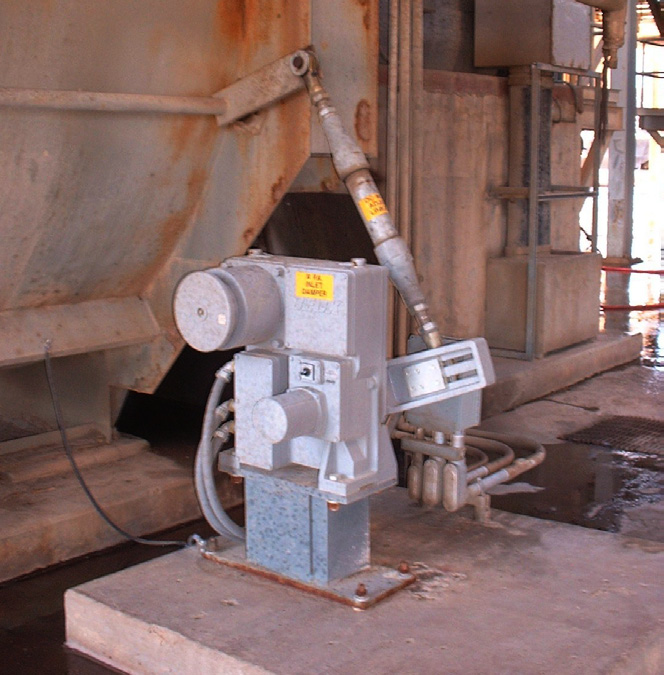
Reheat Damper Upgrades Improve Boiler Efficiency
A JEA power station, which operates two of the largest Circulating Fluidized Bed (CFB) combustors in use, recently completed a plant upgrade to improve efficiency and reduce maintenance costs. A large part of this project focused on improving steam temperature control. Beck high torque 22-409 actuators were installed on the critical Reheat damper applications to provide the precision and reliability required.
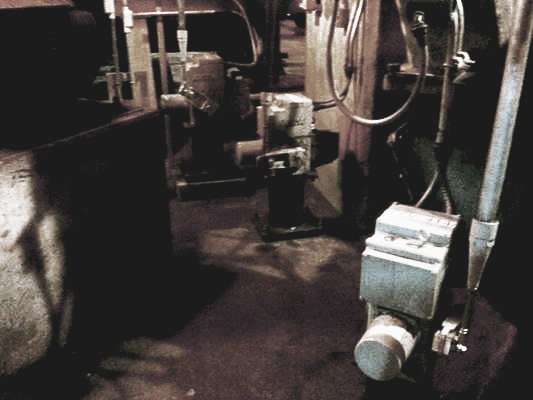
Actuator Upgrades on Coal and Gas Fired Boilers have saved PPG Industries an estimated $174K in maintenance costs and $250K/yr in fuel costs
PPG Industries is a specialty chemical company that serves the aerospace, architectural and packaging industries, to name a few. In 2006, PPG’s West Virginia facility had an initiative to reduce fuel and maintenance costs associated with its boilers. As part of this initiative, PPG planned to replace their pneumatic actuators over the next few years.

34 Year Old Actuator Returned to Critical Service
The Carmeuse lime plant in Maysville, KY has had Beck actuators installed on most of their important control applications for over 30 years. These include primary air, coal mill air, preheater vents, and kiln ID fans. Many of the units installed during original plant construction in the mid-1970’s are still in service. The plant experienced a torque related problem with a 34 year old actuator on a critical ID fan damper actuator. A new motor was installed, without having to remove the actuator from service, returning the damper to operation quickly.
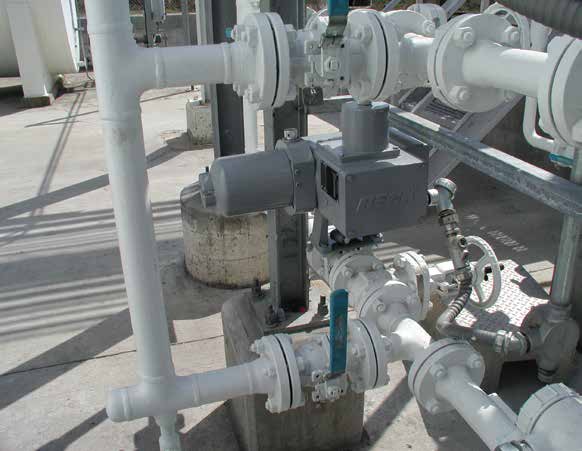
How the installation of a new blend valve actuator has improved operations for one US terminal
The ethanol blending process is a critical part of petrol terminal operation and has a significant impact on product quality, meeting environmental regulations and profitability. Optimising the process is very important, but does present some control challenges. For example, thermal expansion of petrol and ethanol do not occur at the same rate, and the blended mixture has to be isolated from water due to ethanol’s miscibility in water.
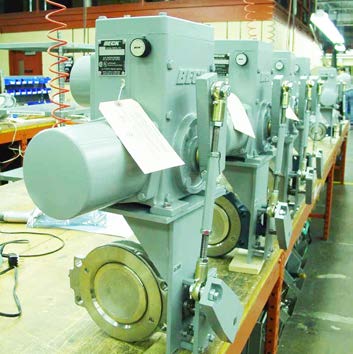
Sludge Valve Upgrades Reduce the Number of Corrective Work Orders
One of the largest wastewater treatment plants in the world recently finished a project for upgrading its sludge valve actuators. In a wastewater treatment process, these valves drain activated sludge from a reservoir and send it to a digester where it is processed. Normal operation of these valves is carried out using a manual handwheel; however, the operation is also commonly accomplished by means of electric, hydraulic or pneumatic actuators.
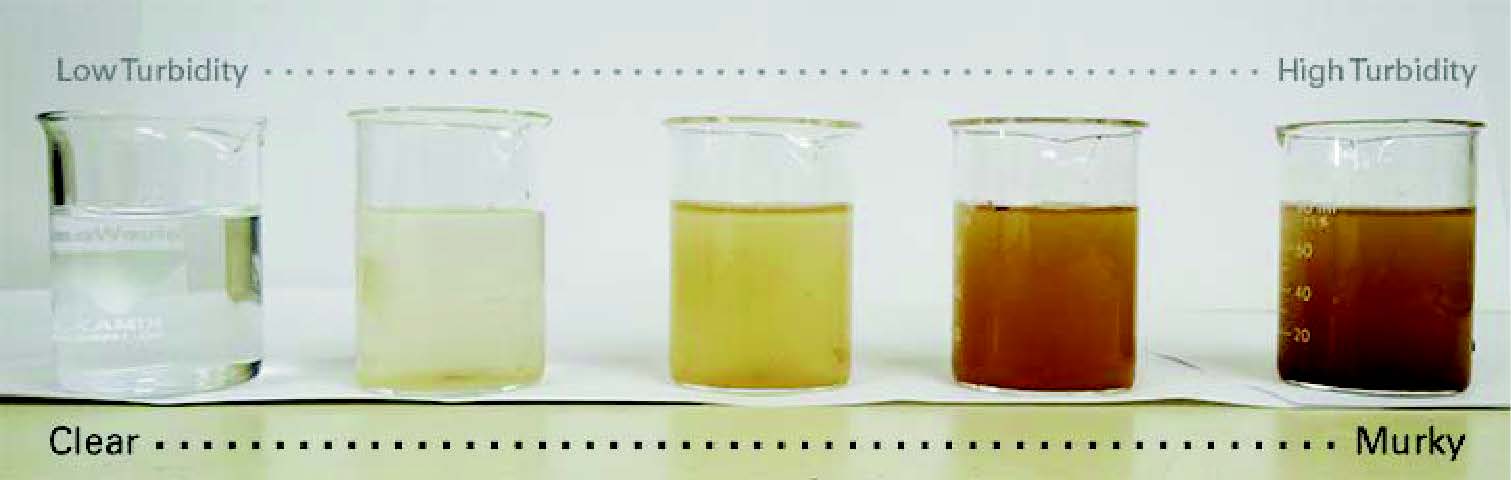
Impact of Improved Actuation on Filter Performance
Moline (IL) Water Filtration Treatment Plant purifies water from the Mississippi River and supplies drinking water to city residents. Plant personnel are constantly working to improve processes in an effort to exceed stringent state and federal regulations. The plant removes particulate matter from the river water using eight mixed media rapid gravity filters.
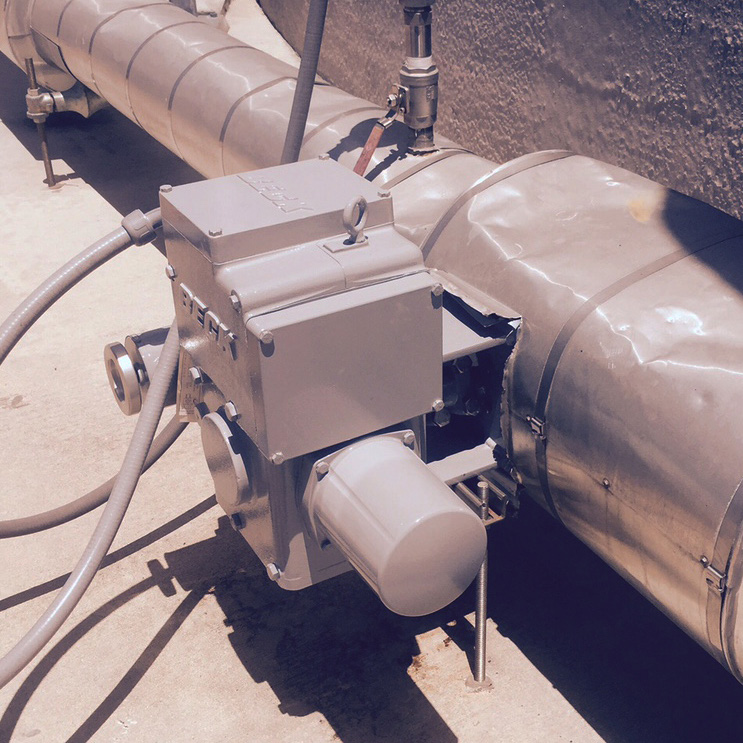
Actuators on Aeration Blower Valves Improve Dissolved Oxygen and Increase Overall Process Stability
The City of Stuart Advanced Water Reclamation Facility is a wastewater treatment plant that produces near-potable, reclaimed water for irrigation uses in South FL. The plant was built in 1955 and most recently upgraded in 2011. The treatment process includes a Dissolved Oxygen System with (3) Aeration Basins. Installing Beck electric actuators on the aeration blower control valves has improved process stability and plant operations.